By Matt Shipman
Researchers have created and demonstrated a new vascular metamaterial that can be reconfigured to modify its thermal and electromagnetic properties.
“We drew inspiration from the network of tiny vessels found in living organisms and have incorporated such microvasculature into a structural epoxy reinforced with glass fibers —essentially vascularized fiberglass,” says Dr. Jason Patrick, corresponding author of the research paper. “And we can control multiple characteristics of the composite material by pumping different fluids through that vasculature. This reconfigurability is appealing for applications ranging from aircraft to buildings to microprocessors.”
Patrick is an assistant professor of civil, construction and environmental engineering at North Carolina State University.
The metamaterial is made using 3D printing technologies. This allows engineers to create networks of tiny tubes, known as microvasculature, in a wide variety of shapes and sizes. The microvasculature can be incorporated into a range of structural composites, from fiberglass to carbon fiber to other high-strength materials for body armor.
In experiments, the researchers infused the vasculature with a room-temperature liquid metal alloy of gallium and indium. This allows researchers to control the electromagnetic properties of the metamaterial by manipulating the microvessel architecture. Specifically, controlling the orientation, spacing and conductive liquid metal contained within the vasculature gives control over how the material filters out specific electromagnetic waves in the radio frequency spectrum. This reconfiguration holds potential for tunable communications and sensing systems, such as RADAR and Wi-Fi, capable of operating in different parts of the spectrum on demand.
“The ability to dynamically reconfigure electromagnetic behavior is really valuable, particularly in applications where size, weight, and power constraints highly incentivize the use of devices which can perform multiple communication and sensing roles within a system,” says co-author Kurt Schab, an assistant professor of electrical engineering at Santa Clara University.
The researchers also circulated water through the same vasculature and demonstrated that they could manipulate the material’s thermal characteristics.
“This could help us develop more efficient active-cooling systems in devices such as electric vehicles, hypersonic aircraft and microprocessors,” Patrick says. “For example, batteries in electric vehicles currently rely on aluminum fins with simple microchannels for cooling. We believe our metamaterial would be as effective at dissipating heat and could also maintain structural protection of the power source – but would be substantially lighter. In addition, 3D printing allows us to create more complex, optimized vascular architectures.”
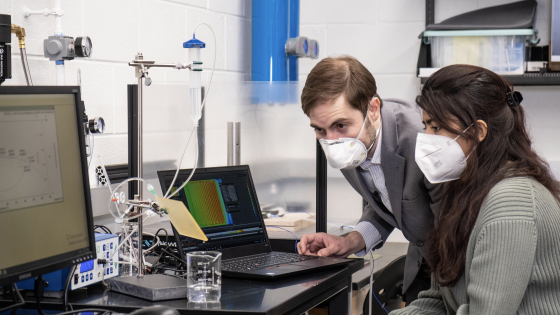
The researchers also note that the new metamaterial should be cost effective as it relies on readily available composite fabrication processes.
“Fiber-reinforced composites are already in widespread use,” Patrick says. “What we’re doing is making material advancements and leveraging 3D printing to create a new class of multifunctional and reconfigurable metamaterials that has real potential for scalable, structural implementation and shouldn’t be prohibitively expensive.”
What’s next?
“We clearly have some applications in mind for this metamaterial, but there are certainly applications we haven’t thought of,” Patrick says. “We are open to working with folks who have fresh ideas on how we might be able to make further use of this novel material.”
The paper, “A Microvascular-based Multifunctional and Reconfigurable Metamaterial,” is published in the journal Advanced Materials Technologies. First author is Urmi Devi, a Ph.D. student at NC State. The paper was co-authored by Zachary Phillips, a Ph.D. student at NC State; Reza Pejman and Ahmad Najafi of Drexel University; Pengfei Zhang and Soheil Soghrati of Ohio State University; Kalyana B. Nakshatrala of the University of Houston; and Kurt R. Schab of Santa Clara University. The research was conducted with support from the Air Force Office of Scientific Research under grant FA9550-18-1-0048.